Polarization-Maintaining FC/PC Fiber Optic Patch Cables
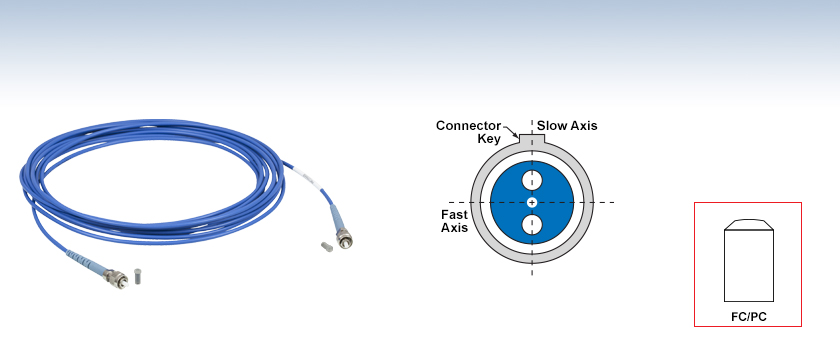
- Polarization-Maintaining Fiber with FC/PC Connectors on Both Ends
- Available in Wavelength Ranges from 400 to 2200 nm
- Custom Connector and Length Options Available
P1-1310PM-FC-5
Connector Key Aligned to Slow Axis1310 nm PM Patch Cable, FC/PC, 5 m Long
Please Wait
PM Fiber Patch Cable Selection Guide |
---|
FC/PC to FC/PC |
FC/APC to FC/APC |
FC/PC to FC/APC Hybrid |
High-ER Cables FC/PC, FC/APC, and Hybrid |
AR-Coated FC/PC and Hybrid |
Dispersion-Compensating FC/APC |
HR-Coated FC/PC and FC/APC |
Features
- Narrow Key (2.0 mm) Aligned to Slow Axis
- Typical Return Loss of 50 dB (40 dB Min)
- Ceramic Radiused Ferrules (UPC)
- Ø3 mm Protective Outer Jacket
- Custom Patch Cables Available
These polarization-maintaining fiber optic patch cables are terminated on both ends with high-quality, narrow key, ceramic FC/PC connectors. These cables are available from stock and feature a high-quality polish, which leads to a typical return loss of 50 dB. Manufactured in our facility, each cable is individually tested* to ensure the specified extinction ratio and insertion loss at fiber-to-fiber junctions. These measurements are available for individual patch cables by contacting Tech Support.
Each patch cable includes two protective caps that shield the ferrule ends from dust and other hazards. Additional CAPF Plastic Fiber Caps and CAPFM Metal Threaded Fiber Caps for FC/PC-terminated ends are also sold separately. Mating sleeves are also available to connect fibers with matching connectors. These mating sleeves minimize back reflections and ensure proper alignment of fiber cores.
*Please note that the port "A" mentioned in the inspection report refers to the end of the patch cable with a white label attached to it.
Item # Prefix | P1-405BPM-FC | P1-488PM-FC | P1-630PM-FC | P1-780PM-FC | P1-980PM-FC |
---|---|---|---|---|---|
Alignment Wavelength | 405 nm | 488 nm | 630 nm | 780 nm | 980 nm |
Fiber Specs | |||||
Fiber Type | PM-S405-XP (PANDA) | PM460-HP (PANDA) | PM630-HP (PANDA) | PM780-HP (PANDA) | PM980-XP (PANDA) |
Operating Wavelength | 400 - 680 nm | 460 - 700 nm | 620 - 850 nm | 770 - 1100 nm | 970 - 1550 nm |
Mode Field Diametera | 3.3 ± 0.5 µm @ 405 nm | 3.3 ± 0.5 µm @ 515 nm | 4.5 ± 0.5 µm @ 630 nm | 5.3 ± 1.0 µm @ 850 nm | 6.6 ± 0.5 µm @ 980 nm |
Numerical Apertureb | 0.12 | 0.12 | 0.12 | 0.12 | 0.12 |
Patch Cable Specs | |||||
Insertion Lossc,d | 1.50 dB (Max) 1.20 dB (Typ.) |
1.50 dB (Max) 1.20 dB (Typ.) |
1.20 dB (Max) 1.00 dB (Typ.) |
1.00 dB (Max) 0.70 dB (Typ.) |
0.70 dB (Max) 0.50 dB (Typ.) |
Extinction Ratioc,d | 15 dB (Min) 17 dB (Typ.) |
18 dB (Min) 20 dB (Typ.) |
20 dB (Min) 22 dB (Typ.) |
20 dB (Min) 22 dB (Typ.) |
22 dB (Min) 24 dB (Typ.) |
Optical Return Lossc | 50 dB Typical | ||||
Connector Type | FC/PC | ||||
Key Width | 2.00 ± 0.02 mm (Narrow Key) | ||||
Slow Axis Alignment | Aligned to Connector Keye | ||||
Cable Length | 1.0 m for Item Numbers Ending in -1 2.0 m for Item Numbers Ending in -2 5.0 m for Item Numbers Ending in -5 10.0 m for Item Numbers Ending in -10 |
||||
Cable Length Tolerance | +0.075/-0 m | ||||
Jacket Type | Ø3 mm Blue PVC Furcation Tubing | ||||
Operating Temperature | 0 to 70 °C | ||||
Storage Temperature | -45 to 85 °C |
Item # Prefix | P1-1064PM-FC | P1-1310PM-FC | P1-1550PM-FC | P1-2000PM-FC |
---|---|---|---|---|
Alignment Wavelength | 1064 nm | 1310 nm | 1550 nm | 2000 nm |
Fiber Specs | ||||
Fiber Type | PM980-XP (PANDA) | PM1300-XP (PANDA) | PM1550-XP (PANDA) | PM2000 (PANDA) |
Operating Wavelength | 970 - 1550 nm | 1270 - 1625 nm | 1440 - 1625 nm | 1850 - 2200 nm |
Mode Field Diametera | 6.6 ± 0.5 μm @ 980 nm | 9.3 ± 0.5 µm @ 1300 nm | 10.1 ± 0.4 µm @ 1550 nm | 8.0 µm @ 1950 nm |
Numerical Apertureb | 0.12 | 0.12 | 0.125 | 0.20 |
Patch Cable Specs | ||||
Insertion Lossc,d | 0.70 dB (Max) 0.50 dB (Typ.) |
0.50 dB (Max) 0.30 dB (Typ.) |
0.50 dB (Max) 0.30 dB (Typ.) |
0.50 dB (Max) 0.30 dB (Typ.) |
Extinction Ratioc,d | 22 dB (Min) 24 dB (Typ.) |
23 dB (Min) 25 dB (Typ.) |
23 dB (Min) 25 dB (Typ.) |
23 dB (Min) 25 dB (Typ.) |
Optical Return Lossc | 50 dB Typical | |||
Connector Type | FC/PC | |||
Key Width | 2.00 mm ± 0.02 (Narrow Key) | |||
Slow Axis Alignment | Aligned to Connector Keye | |||
Cable Length | 1.0 m for Item Numbers Ending in -1 2.0 m for Item Numbers Ending in -2 5.0 m for Item Numbers Ending in -5 |
|||
Cable Length Tolerance | +0.075/-0 m | |||
Jacket Type | Ø3 mm Blue PVC Furcation Tubing | |||
Operating Temperature | 0 to 70 °C | |||
Storage Temperature | -45 to 85 °C |
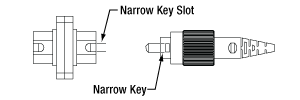
Click to Enlarge
Mating Between a Narrow-Key Mating Sleeve and Connector
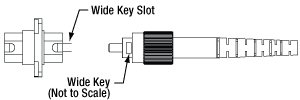
Click to Enlarge
Mating Between a Wide-Key Mating Sleeve and Connector
FC/PC and FC/APC Patch Cable Key Alignment
FC/PC and FC/APC Patch Cables are equipped with either a 2.0 mm narrow or 2.2 mm wide alignment key that fits into a corresponding slot on a mated component. These keys and slots are essential to correctly align the cores of connected fiber patch cables and minimize the insertion loss of the connection.
As an example, Thorlabs designs and manufactures mating sleeves for FC/PC- and FC/APC-terminated patch cables to precise specifications that ensure good alignment when used correctly. To ensure the best alignment, the alignment key on the patch cable is inserted into the corresponding narrow or wide-key slot on the mating sleeve.
Wide-Key-Slot Mating Sleeves
2.2 mm wide-key-slot mating sleeves are compatible with both wide-key and narrow-key connectors. However, using a narrow-key connector in a wide-key slot will allow the connector to rotate slightly in the mating sleeve (as shown in the animation below and to the left). While this configuration is acceptable for patch cables with FC/PC connectors, for FC/APC applications, we recommend using narrow-key-slot mating sleeves to ensure optimum alignment.
Narrow-Key-Slot Mating Sleeves
2.0 mm narrow-key-slot mating sleeves allow for optimal alignment of angled, narrow-key FC/APC connectors, as shown in the animation below and to the right. Therefore, they are not compatible with connectors that have a 2.2 mm wide key. Please note that all FC/PC and FC/APC patch cables manufactured by Thorlabs use narrow key connectors.
Once a narrow key connector is inserted into a narrow-key-slot mating sleeve, the connector will not rotate. We therefore recommend these mating sleeves for FC/PC and FC/APC connectors with narrow keys.
When a narrow key connector is inserted into a wide-key-slot mating sleeve, the connector has room to rotate. For narrow key FC/PC connectors, this is acceptable, but for narrow key FC/APC connectors, significant coupling losses will result.
Quick Links |
---|
Damage at the Air / Glass Interface |
Intrinsic Damage Threshold |
Preparation and Handling of Optical Fibers |
Laser-Induced Damage in Silica Optical Fibers
The following tutorial details damage mechanisms relevant to unterminated (bare) fiber, terminated optical fiber, and other fiber components from laser light sources. These mechanisms include damage that occurs at the air / glass interface (when free-space coupling or when using connectors) and in the optical fiber itself. A fiber component, such as a bare fiber, patch cable, or fused coupler, may have multiple potential avenues for damage (e.g., connectors, fiber end faces, and the device itself). The maximum power that a fiber can handle will always be limited by the lowest limit of any of these damage mechanisms.
While the damage threshold can be estimated using scaling relations and general rules, absolute damage thresholds in optical fibers are very application dependent and user specific. Users can use this guide to estimate a safe power level that minimizes the risk of damage. Following all appropriate preparation and handling guidelines, users should be able to operate a fiber component up to the specified maximum power level; if no maximum is specified for a component, users should abide by the "practical safe level" described below for safe operation of the component. Factors that can reduce power handling and cause damage to a fiber component include, but are not limited to, misalignment during fiber coupling, contamination of the fiber end face, or imperfections in the fiber itself. For further discussion about an optical fiber’s power handling abilities for a specific application, please contact Thorlabs’ Tech Support.

Click to Enlarge
Undamaged Fiber End
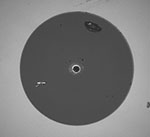
Click to Enlarge
Damaged Fiber End
Damage at the Air / Glass Interface
There are several potential damage mechanisms that can occur at the air / glass interface. Light is incident on this interface when free-space coupling or when two fibers are mated using optical connectors. High-intensity light can damage the end face leading to reduced power handling and permanent damage to the fiber. For fibers terminated with optical connectors where the connectors are fixed to the fiber ends using epoxy, the heat generated by high-intensity light can burn the epoxy and leave residues on the fiber facet directly in the beam path.
Estimated Optical Power Densities on Air / Glass Interfacea | ||
---|---|---|
Type | Theoretical Damage Thresholdb | Practical Safe Levelc |
CW (Average Power) |
~1 MW/cm2 | ~250 kW/cm2 |
10 ns Pulsed (Peak Power) |
~5 GW/cm2 | ~1 GW/cm2 |
Damage Mechanisms on the Bare Fiber End Face
Damage mechanisms on a fiber end face can be modeled similarly to bulk optics, and industry-standard damage thresholds for UV Fused Silica substrates can be applied to silica-based fiber. However, unlike bulk optics, the relevant surface areas and beam diameters involved at the air / glass interface of an optical fiber are very small, particularly for coupling into single mode (SM) fiber. therefore, for a given power density, the power incident on the fiber needs to be lower for a smaller beam diameter.
The table to the right lists two thresholds for optical power densities: a theoretical damage threshold and a "practical safe level". In general, the theoretical damage threshold represents the estimated maximum power density that can be incident on the fiber end face without risking damage with very good fiber end face and coupling conditions. The "practical safe level" power density represents minimal risk of fiber damage. Operating a fiber or component beyond the practical safe level is possible, but users must follow the appropriate handling instructions and verify performance at low powers prior to use.
Calculating the Effective Area for Single Mode Fibers
The effective area for single mode (SM) fiber is defined by the mode field diameter (MFD), which is the cross-sectional area through which light propagates in the fiber; this area includes the fiber core and also a portion of the cladding. To achieve good efficiency when coupling into a single mode fiber, the diameter of the input beam must match the MFD of the fiber.
As an example, SM400 single mode fiber has a mode field diameter (MFD) of ~Ø3 µm operating at 400 nm, while the MFD for SMF-28 Ultra single mode fiber operating at 1550 nm is Ø10.5 µm. The effective area for these fibers can be calculated as follows:
SM400 Fiber: Area = Pi x (MFD/2)2 = Pi x (1.5 µm)2 = 7.07 µm2 = 7.07 x 10-8 cm2
SMF-28 Ultra Fiber: Area = Pi x (MFD/2)2 = Pi x (5.25 µm)2 = 86.6 µm2 = 8.66 x 10-7 cm2
To estimate the power level that a fiber facet can handle, the power density is multiplied by the effective area. Please note that this calculation assumes a uniform intensity profile, but most laser beams exhibit a Gaussian-like shape within single mode fiber, resulting in a higher power density at the center of the beam compared to the edges. Therefore, these calculations will slightly overestimate the power corresponding to the damage threshold or the practical safe level. Using the estimated power densities assuming a CW light source, we can determine the corresponding power levels as:
SM400 Fiber: 7.07 x 10-8 cm2 x 1 MW/cm2 = 7.1 x 10-8 MW = 71 mW (Theoretical Damage Threshold)
7.07 x 10-8 cm2 x 250 kW/cm2 = 1.8 x 10-5 kW = 18 mW (Practical Safe Level)
SMF-28 Ultra Fiber: 8.66 x 10-7 cm2 x 1 MW/cm2 = 8.7 x 10-7 MW = 870 mW (Theoretical Damage Threshold)
8.66 x 10-7 cm2 x 250 kW/cm2 = 2.1 x 10-4 kW = 210 mW (Practical Safe Level)
Effective Area of Multimode Fibers
The effective area of a multimode (MM) fiber is defined by the core diameter, which is typically far larger than the MFD of an SM fiber. For optimal coupling, Thorlabs recommends focusing a beam to a spot roughly 70 - 80% of the core diameter. The larger effective area of MM fibers lowers the power density on the fiber end face, allowing higher optical powers (typically on the order of kilowatts) to be coupled into multimode fiber without damage.
Damage Mechanisms Related to Ferrule / Connector Termination
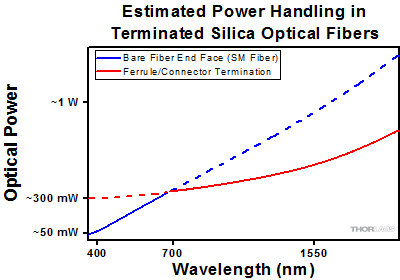
Plot showing approximate input power that can be incident on a single mode silica optical fiber with a termination. Each line shows the estimated power level due to a specific damage mechanism. The maximum power handling is limited by the lowest power level from all relevant damage mechanisms (indicated by a solid line).
Fibers terminated with optical connectors have additional power handling considerations. Fiber is typically terminated using epoxy to bond the fiber to a ceramic or steel ferrule. When light is coupled into the fiber through a connector, light that does not enter the core and propagate down the fiber is scattered into the outer layers of the fiber, into the ferrule, and the epoxy used to hold the fiber in the ferrule. If the light is intense enough, it can burn the epoxy, causing it to vaporize and deposit a residue on the face of the connector. This results in localized absorption sites on the fiber end face that reduce coupling efficiency and increase scattering, causing further damage.
For several reasons, epoxy-related damage is dependent on the wavelength. In general, light scatters more strongly at short wavelengths than at longer wavelengths. Misalignment when coupling is also more likely due to the small MFD of short-wavelength SM fiber that also produces more scattered light.
To minimize the risk of burning the epoxy, fiber connectors can be constructed to have an epoxy-free air gap between the optical fiber and ferrule near the fiber end face. Our high-power multimode fiber patch cables use connectors with this design feature.
Determining Power Handling with Multiple Damage Mechanisms
When fiber cables or components have multiple avenues for damage (e.g., fiber patch cables), the maximum power handling is always limited by the lowest damage threshold that is relevant to the fiber component. In general, this represents the highest input power that can be incident on the patch cable end face and not the coupled output power.
As an illustrative example, the graph to the right shows an estimate of the power handling limitations of a single mode fiber patch cable due to damage to the fiber end face and damage via an optical connector. The total input power handling of a terminated fiber at a given wavelength is limited by the lower of the two limitations at any given wavelength (indicated by the solid lines). A single mode fiber operating at around 488 nm is primarily limited by damage to the fiber end face (blue solid line), but fibers operating at 1550 nm are limited by damage to the optical connector (red solid line).
In the case of a multimode fiber, the effective mode area is defined by the core diameter, which is larger than the effective mode area for SM fiber. This results in a lower power density on the fiber end face and allows higher optical powers (on the order of kilowatts) to be coupled into the fiber without damage (not shown in graph). However, the damage limit of the ferrule / connector termination remains unchanged and as a result, the maximum power handling for a multimode fiber is limited by the ferrule and connector termination.
Please note that these are rough estimates of power levels where damage is very unlikely with proper handling and alignment procedures. It is worth noting that optical fibers are frequently used at power levels above those described here. However, these applications typically require expert users and testing at lower powers first to minimize risk of damage. Even still, optical fiber components should be considered a consumable lab supply if used at high power levels.
Intrinsic Damage Threshold
In addition to damage mechanisms at the air / glass interface, optical fibers also display power handling limitations due to damage mechanisms within the optical fiber itself. These limitations will affect all fiber components as they are intrinsic to the fiber itself. Two categories of damage within the fiber are damage from bend losses and damage from photodarkening.
Bend Losses
Bend losses occur when a fiber is bent to a point where light traveling in the core is incident on the core/cladding interface at an angle higher than the critical angle, making total internal reflection impossible. Under these circumstances, light escapes the fiber, often in a localized area. The light escaping the fiber typically has a high power density, which burns the fiber coating as well as any surrounding furcation tubing.
A special category of optical fiber, called double-clad fiber, can reduce the risk of bend-loss damage by allowing the fiber’s cladding (2nd layer) to also function as a waveguide in addition to the core. By making the critical angle of the cladding/coating interface higher than the critical angle of the core/clad interface, light that escapes the core is loosely confined within the cladding. It will then leak out over a distance of centimeters or meters instead of at one localized spot within the fiber, minimizing the risk of damage. Thorlabs manufactures and sells 0.22 NA double-clad multimode fiber, which boasts very high, megawatt range power handling.
Photodarkening
A second damage mechanism, called photodarkening or solarization, can occur in fibers used with ultraviolet or short-wavelength visible light, particularly those with germanium-doped cores. Fibers used at these wavelengths will experience increased attenuation over time. The mechanism that causes photodarkening is largely unknown, but several fiber designs have been developed to mitigate it. For example, fibers with a very low hydroxyl ion (OH) content have been found to resist photodarkening and using other dopants, such as fluorine, can also reduce photodarkening.
Even with the above strategies in place, all fibers eventually experience photodarkening when used with UV or short-wavelength light, and thus, fibers used at these wavelengths should be considered consumables.
Preparation and Handling of Optical Fibers
General Cleaning and Operation Guidelines
These general cleaning and operation guidelines are recommended for all fiber optic products. Users should still follow specific guidelines for an individual product as outlined in the support documentation or manual. Damage threshold calculations only apply when all appropriate cleaning and handling procedures are followed.
-
All light sources should be turned off prior to installing or integrating optical fibers (terminated or bare). This ensures that focused beams of light are not incident on fragile parts of the connector or fiber, which can possibly cause damage.
-
The power-handling capability of an optical fiber is directly linked to the quality of the fiber/connector end face. Always inspect the fiber end prior to connecting the fiber to an optical system. The fiber end face should be clean and clear of dirt and other contaminants that can cause scattering of coupled light. Bare fiber should be cleaved prior to use and users should inspect the fiber end to ensure a good quality cleave is achieved.
-
If an optical fiber is to be spliced into the optical system, users should first verify that the splice is of good quality at a low optical power prior to high-power use. Poor splice quality may increase light scattering at the splice interface, which can be a source of fiber damage.
-
Users should use low power when aligning the system and optimizing coupling; this minimizes exposure of other parts of the fiber (other than the core) to light. Damage from scattered light can occur if a high power beam is focused on the cladding, coating, or connector.
Tips for Using Fiber at Higher Optical Power
Optical fibers and fiber components should generally be operated within safe power level limits, but under ideal conditions (very good optical alignment and very clean optical end faces), the power handling of a fiber component may be increased. Users must verify the performance and stability of a fiber component within their system prior to increasing input or output power and follow all necessary safety and operation instructions. The tips below are useful suggestions when considering increasing optical power in an optical fiber or component.
-
Splicing a fiber component into a system using a fiber splicer can increase power handling as it minimizes possibility of air/fiber interface damage. Users should follow all appropriate guidelines to prepare and make a high-quality fiber splice. Poor splices can lead to scattering or regions of highly localized heat at the splice interface that can damage the fiber.
-
After connecting the fiber or component, the system should be tested and aligned using a light source at low power. The system power can be ramped up slowly to the desired output power while periodically verifying all components are properly aligned and that coupling efficiency is not changing with respect to optical launch power.
-
Bend losses that result from sharply bending a fiber can cause light to leak from the fiber in the stressed area. When operating at high power, the localized heating that can occur when a large amount of light escapes a small localized area (the stressed region) can damage the fiber. Avoid disturbing or accidently bending fibers during operation to minimize bend losses.
-
Users should always choose the appropriate optical fiber for a given application. For example, large-mode-area fibers are a good alternative to standard single mode fibers in high-power applications as they provide good beam quality with a larger MFD, decreasing the power density on the air/fiber interface.
-
Step-index silica single mode fibers are normally not used for ultraviolet light or high-peak-power pulsed applications due to the high spatial power densities associated with these applications.
Insights into Polarization Conventions
Scroll down to read about:
- Labels Used to Identify Perpendicular and Parallel Components
Click here for more insights into lab practices and equipment.
Labels Used to Identify Perpendicular and Parallel Components
When polarized light is incident on a surface, it is often described in terms of perpendicular and parallel components. These are orthogonal to each other and the direction in which the light is propagating (Figure 1).
Labels and symbols applied to the perpendicular and parallel components can make it difficult to determine which is which. The table identifies, for a variety of different sets, which label refers to the perpendicular component and which to the parallel.
Labels | Notes |
|
---|---|---|
Perpendicular | Parallel | |
s | p | Senkrecht (s) is 'perpendicular' in German. Parallel begins with 'p.' |
TE | TM | TE: Transverse electric field. |
⊥ | // | ⊥ and // are symbols for perpendicular and parallel, respectively. |
σ | π | The Greek letters corresponding to s and p are σ and π, respectively. |
Sagittal | Tangential | A sagittal plane is a longitudinal plane that divides a body. |
The perpendicular and parallel directions are referenced to the plane of incidence, which is illustrated in Figure 1 for a beam reflecting from a surface. Together, the incident ray and the surface normal define the plane of incidence, and the incident and reflected rays are both contained in this plane. The perpendicular direction is normal to the plane of incidence, and the parallel direction is in the plane of incidence.
The electric fields of the perpendicular and parallel components oscillate in planes that are orthogonal to one another. The electric field of the perpendicular component oscillates in a plane perpendicular to the plane of incidence, while the electric field of the parallel component oscillated in the plane of incidence. The polarization of the light beam is the vector sum of the perpendicular and parallel components.
Normally Incident Light
Since a plane of incidence cannot be defined for normally incident light, this approach cannot be used to unambiguously define perpendicular and parallel components of light. There is limited need to make the distinction, since under conditions of normal incidence the reflectivity is the same for all components of light.
Date of Last Edit: Mar. 5, 2020
Posted Comments: | |
广 李
 (posted 2024-07-11 11:13:07.933) 你好 我想知道该款产品的热光系数和热膨胀系数 jdelia
 (posted 2024-07-19 02:41:03.0) Thank you for contacting Thorlabs. Your feedback translated is: "Hello, I would like to know the thermo-optical coefficient and thermal expansion coefficient of this product." We are reaching out to you directly to further discuss your application. Jose Mejia
 (posted 2024-02-05 13:49:25.737) Hi, we were considering to use one of the PM fibers to couple single photons from a SPDC process, where we have diagonally polarized photons. What would be the best way to couple these photons into the fiber? In what direction should we align the axis? Thank you! cdolbashian
 (posted 2024-02-16 04:19:24.0) Thank you for reaching out to us. We align our slow axis to the key of the fiber. For diagonally polarized photons, you would want to align them to either the fast or slow axis, not between. You can either align your key to the polarization of your SPDC, or simply use a combination of polarizer and half wave plate to rotate your polarization state. I have contacted you directly to discuss this. Ertuğrul İnciel
 (posted 2023-10-05 15:12:24.517) Hi, what is the best way to couple light into PM fiber. How can we make sure that polarization of light matches one of the axes. Should we use some polarization rotating optic for linearly polarized light before fiber. Thank you in advance, best regards. jdelia
 (posted 2023-10-13 08:23:52.0) For coupling into a single mode fiber optic, we suggest using a coupling optic with several degrees of kinematic control, such as one of our FiberPort Collimators / Couplers: https://www.thorlabs.com/newgrouppage9.cfm?objectgroup_id=2940. We have a calculator under the "Selection Guide" tab on that page to help determine the best FiberPort for a particular fiber. We have a written tutorial under the "Alignment Procedure" tab and some video tutorials on fiber alignment under our Video Insights: https://www.thorlabs.com/newgrouppage9.cfm?objectgroup_id=14062.I have also contacted you directly to discuss your application further. user
 (posted 2023-02-24 15:33:12.89) If the key in connector to the pm fiber is secured in one place aligned to the slow axis, how to input linear polarization at different angles into the fiber? jgreschler
 (posted 2023-02-24 11:18:10.0) Thank you for reaching out to Thorlabs. Polarization maintaining fibers will only effectively maintain linear polarization states aligned with the fast or slow axis of the fiber, they will not maintain any other linear state with angle between the two axes. I have reached out to you directly to discuss this application further. mo Zohrabi
 (posted 2022-05-10 10:58:26.28) Hi there,
I am research scientist at ECEE department at CU Boulder. We have performed an optical experiment on PM-980 fiber for temperature sensing and we are working on a simulation to compare it with our experimental results. I am wondering if you can share the dimensions of the stress rod/core and their refractive indices as well as the birefringence. I am happy to sign a NDA if necessary.
Best,
Mo jgreschler
 (posted 2022-05-10 12:01:51.0) Thank you for reaching out to Thorlabs. These data are available on request by emailing techsupport@thorlabs.com. I have reached out to you directly with information. Michael Sym
 (posted 2021-09-29 13:45:43.427) Hello, could you provide the NA of the fibers as the divergence at the 1/e^2 intensity? Also, the MFD is the measured nominal value? Could you please explain the procedure for specifying this property?
Thank you in advance. cdolbashian
 (posted 2021-10-05 05:00:42.0) Thank you for contacting us at Thorlabs. The divergence angle can be calculated for SM/PM fibers following this helpful article on our website: https://www.thorlabs.com/newgrouppage9.cfm?objectgroup_id=12211&tabname=Fiber%20Optics#SMFiberCoupling and see the article "Does NA provide a good estimate of beam divergence from a single mode fiber?"
The stated MFD is indeed the nominal value.
The procedure and instrumentation varies from vendor to vendor, but it involves the Petermann II far field measurement.
I hope this helps! Mika C
 (posted 2021-02-05 11:46:44.32) What is the core diameter of the PM98-XP fiber? I don't see this spec listed anywhere. YLohia
 (posted 2021-02-05 02:07:59.0) Hello Mika, the mode field diameter of this fiber is listed in the Specs tab as 6.6 ± 0.5 µm @ 980 nm. exr007
 (posted 2018-10-03 09:17:31.633) I am not too familiar with PM fibres, therefore I was hoping I could ask whether they are capable of maintaining circularly polarized light or just linearly polarized light?
Thanks YLohia
 (posted 2018-10-04 09:42:46.0) Hello, thank you for contacting Thorlabs. PM fibers are not capable of maintaining circularly polarized light. They are designed to only maintain a linear polarization state aligned to the slow axis of the fiber. katja.severin
 (posted 2017-08-25 08:21:32.357) I would like to know which core types (material) have the fibers P1-630PM-FC-2 and P1-1064PM-FC-2? Is it pure silica? nbayconich
 (posted 2017-08-28 05:50:59.0) Thank you for contacting Thorlabs. Both of these fibers have GeO2 doped SiO2 cores. eddie.ross
 (posted 2017-01-31 14:20:21.067) We are looking at using the fibers within a radiation environment, would you be able to comment at all on the radiation damage effects on the performance?
In addition, to aid our research, could you please specify the glass type used in the fibers?
Thanks pbui
 (posted 2017-01-31 09:39:19.0) Thank you for your inquiry. We do not have any information regarding how radiation affects our patch cables as it's not something we're able to test. The glass type used in our polarization maintaining fibers is silica. Depending on the fiber type, there may also be dopants such as fluorine or germanium. dubec
 (posted 2015-07-10 09:29:32.663) Hello, regarding the P1-405BPM-FC-2 fiber, I am not sure after I read your "damage threshold" instructions, what is the maximum power limit. From the graph I would say 50mW, because it is a terminated cable. If not terminated, the limit would be 11.3mW, right? The main question is as follows: if I use 100mW 405nm diode and I focus is to 10um diameter, will I damage the fiber end or not? Thank you! besembeson
 (posted 2015-09-23 10:22:50.0) Response from Bweh at Thorlabs USA: If not terminated, the limit will be 25mW. 10um diameter gives 78um^2 area which gives ~196mW using the practical safe value. But if you are coupling into the fiber, the mode field diameter is ~3.6um which leads to 10um^2 or a safe power limit of 25mW. jmflores
 (posted 2013-07-02 11:17:39.477) Hi. I bought nine months ago (by October) a polarization maintaining patch cable (P1-405PM-FC-2). According with on-line datasheet, the operating wavelength is 400-680nm but in the test datasheet coming with the fiber said 400-500 nm, why this difference? Which problems I will have if I pretend to use this fiber at 682nm? pbui
 (posted 2013-07-03 15:55:00.0) Response from Phong at Thorlabs: Thank you for your feedback. The operating wavelength in your data sheet was listed in error. We have corrected this mistake. The Fiber's Operating Wavelength is indeed 400-680 nm. Please also note that the P1-405PM-FC-2 was aligned and tested at 405 nm, which is now also indicated on the data sheet. tcohen
 (posted 2012-03-09 19:51:00.0) Response from Tim at Thorlabs: Thank you for your feedback. The attenuation for these cables can be found by clicking on the fiber type located directly above the patch cables. By clicking on the "Documents" tab you can access the specification sheet, which has the attenuation in dB/km. rosalest
 (posted 2012-03-09 18:32:55.0) What is the maximum attenuation for these path cables in dB/km. Is it the same as for the regular single mode patch cables? sharrell
 (posted 2011-08-24 16:56:00.0) A Response from Sean at Thorlabs: Thank you for your feedback. I have added the nominal numerical aperture to all of our PM fiber patch cable pages. These values may be found by clicking on the Specs tab of each page. Complete fiber specifications may also be found by clicking on the fiber part number listed in the Specs table. user
 (posted 2011-08-24 10:57:00.0) What is the NA of these fibers? I plan to connect this to a fixed fiber collimation package (F280APC-A, NA = 0.15). To have higher than 50% coupling efficiency into that, I am expecting this PM fiber to have NA ~0.15 which is similar to the non-PM SMF. kenlee
 (posted 2009-12-10 12:16:43.0) A response from Ken at Thorlabs:
3W is too much for these cables. The epoxy used to glue the connector will not withstand that and it will burn the fiber and connector. We usually recommend 300mW as the maximum power. user
 (posted 2009-12-10 08:13:51.0) Is it possible to use the P1-488PM-FC-5 with a 3 watts argon laser at 488nm (continues)? Or could there be issues with the power? Laurie
 (posted 2008-04-25 08:27:58.0) Response from Laurie at Thorlabs to j.d.ellis: Thorlabs does offer PM patch cables for 633 nm. Any of the following PM fibers, which all operate at that wavelength, can be ordered as patch cables: PM630-HP, HB600, or PM-S630-HP. We would just need to know what length, jacket, and connector you require. In addition, we offer 24-hour turnaround on stocked items. Please call our tech support staff for pricing and to specify your requirements (973-579-7227). j.d.ellis
 (posted 2008-04-25 03:34:47.0) Do you have any patch cables for PM fibers for 633nm wavelength? I find it ridiculous that you have the couplers for 633 but not the fiber... |

Item # | Alignment Wavelength |
Fiber Type | Operating Wavelength |
Cutoff Wavelength |
Extinction Ratioa,b |
Insertion Lossa,b |
Mode Field Diameterc | Jacket | Length |
---|---|---|---|---|---|---|---|---|---|
P1-405BPM-FC-1 | 405 nm | PM-S405-XP (PANDA) |
400 - 680 nm | 380 ± 20 nm | 15 dB (Min) 17 dB (Typ.) |
1.50 dB (Max) 1.20 dB (Typ.) |
3.3 ± 0.5 µm @ 405 nm | Ø3 mm Blue PVC Furcation Tubing |
1 m |
P1-405BPM-FC-2 | 2 m | ||||||||
P1-405BPM-FC-5 | 5 m |

Item # | Alignment Wavelength |
Fiber Type | Operating Wavelength |
Cutoff Wavelength |
Extinction Ratioa,b |
Insertion Lossa,b |
Mode Field Diameterc | Jacket | Length |
---|---|---|---|---|---|---|---|---|---|
P1-488PM-FC-1 | 488 nm | PM460-HP (PANDA) |
460 - 700 nm | 410 ± 40 nm | 18 dB (Min) 20 dB (Typ.) |
1.50 dB (Max) 1.20 dB (Typ.) |
3.3 ± 0.5 µm @ 515 nm | Ø3 mm Blue PVC Furcation Tubing |
1 m |
P1-488PM-FC-2 | 2 m | ||||||||
P1-488PM-FC-5 | 5 m |

Item # | Alignment Wavelength |
Fiber Type | Operating Wavelength |
Cutoff Wavelength |
Extinction Ratioa,b |
Insertion Lossa,b |
Mode Field Diameterc | Jacket | Length |
---|---|---|---|---|---|---|---|---|---|
P1-630PM-FC-1 | 630 nm | PM630-HP (PANDA) |
620 - 850 nm | 570 ± 50 nm | 20 dB (Min) 22 dB (Typ.) |
1.20 dB (Max) 1.00 dB (Typ.) |
4.5 ± 0.5 µm @ 630 nm | Ø3 mm Blue PVC Furcation Tubing |
1 m |
P1-630PM-FC-2 | 2 m | ||||||||
P1-630PM-FC-5 | 5 m | ||||||||
P1-630PM-FC-10 | 10 m |

Item # | Alignment Wavelength |
Fiber Type | Operating Wavelength |
Cutoff Wavelength |
Extinction Ratioa,b |
Insertion Lossa,b |
Mode Field Diameterc | Jacket | Length |
---|---|---|---|---|---|---|---|---|---|
P1-780PM-FC-1 | 780 nm | PM780-HP (PANDA) |
770 - 1100 nm | 710 ± 60 nm | 20 dB (Min) 22 dB (Typ.) |
1.00 dB (Max) 0.70 dB (Typ.) |
5.3 ± 1.0 µm @ 850 nm | Ø3 mm Blue PVC Furcation Tubing |
1 m |
P1-780PM-FC-2 | 2 m | ||||||||
P1-780PM-FC-5 | 5 m | ||||||||
P1-780PM-FC-10 | 10 m |

Item # | Alignment Wavelength |
Fiber Type | Operating Wavelength |
Cutoff Wavelength |
Extinction Ratioa,b,c |
Insertion Lossa,c |
Mode Field Diameterd | Jacket | Length |
---|---|---|---|---|---|---|---|---|---|
P1-980PM-FC-2 | 980 nm | PM980-XP (PANDA) |
970 - 1550 nm | 920 ± 50 nm | 22 dB (Min) 24 dB (Typ.) |
0.70 dB (Max) 0.50 dB (Typ.) |
6.6 ± 0.5 µm @ 980 nm | Ø3 mm Blue PVC Furcation Tubing |
2 m |
P1-980PM-FC-5 | 5 m |

Item # | Alignment Wavelength |
Fiber Type | Operating Wavelength |
Cutoff Wavelength |
Extinction Ratioa,b,c |
Insertion Lossa,c |
Mode Field Diameterd | Jacket | Length |
---|---|---|---|---|---|---|---|---|---|
P1-1064PM-FC-2 | 1064 nm | PM980-XP (PANDA) |
970 - 1550 nm | 920 ± 50 nm | 22 dB (Min) 24 dB (Typ.) |
0.70 dB (Max) 0.50 dB (Typ.) |
6.6 ± 0.5 µm @ 980 nm | Ø3 mm Blue PVC Furcation Tubing |
2 m |
P1-1064PM-FC-5 | 5 m |

Item # | Alignment Wavelength |
Fiber Type | Operating Wavelength |
Cutoff Wavelength |
Extinction Ratioa,b,c |
Insertion Lossa,c |
Mode Field Diameterd | Jacket | Length |
---|---|---|---|---|---|---|---|---|---|
P1-1310PM-FC-2 | 1310 nm | PM1300-XP (PANDA) |
1270 - 1625 nm | 1210 ± 60 nm | 23 dB (Min) 25 dB (Typ.) |
0.50 dB (Max) 0.30 dB (Typ.) |
9.3 ± 0.5 µm @ 1300 nm | Ø3 mm Blue PVC Furcation Tubing |
2 m |
P1-1310PM-FC-5 | 5 m |

Item # | Alignment Wavelength |
Fiber Type | Operating Wavelength |
Cutoff Wavelength |
Extinction Ratioa,b,c |
Insertion Lossa,c |
Mode Field Diameterd | Jacket | Length |
---|---|---|---|---|---|---|---|---|---|
P1-1550PM-FC-1 | 1550 nm | PM1550-XP (PANDA) |
1440 - 1625 nm | 1380 ± 60 nm | 23 dB (Min) 25 dB (Typ.) |
0.50 dB (Max) 0.30 dB (Typ.) |
10.1 ± 0.4 µm @ 1550 nm | Ø3 mm Blue PVC Furcation Tubing |
1 m |
P1-1550PM-FC-2 | 2 m | ||||||||
P1-1550PM-FC-5 | 5 m |

Item # | Alignment Wavelength |
Fiber Type | Operating Wavelength |
Cutoff Wavelength |
Extinction Ratioa,b |
Insertion Lossa,b |
Mode Field Diameterc |
Jacket | Length |
---|---|---|---|---|---|---|---|---|---|
P1-2000PM-FC-2 | 2000 nm | PM2000 (PANDA) |
1850 - 2200 nm | 1720 ± 80 nm | 23 dB (Min) 25 dB (Typ.) |
0.50 dB (Max) 0.30 dB (Typ.) |
8.0 µm @ 2200 nm | Ø3 mm Blue PVC Furcation Tubing |
2 m |