Iris Diaphragms Without Mounting Holes
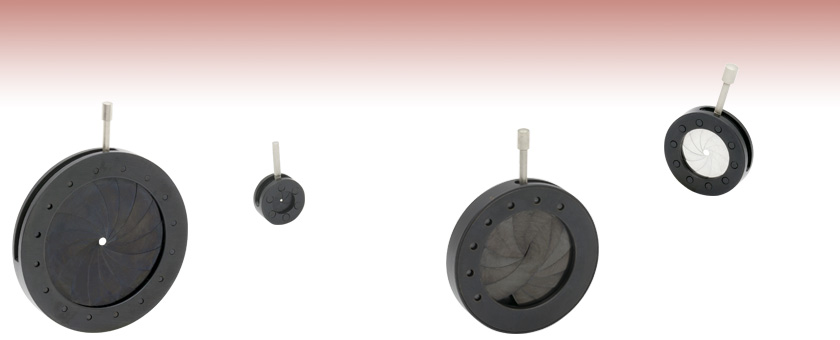
- Continuously Variable Irises
- Maximum Apertures Ranging from Ø5.0 mm to Ø75.0 mm
- Ideal for OEM Applications
- Black and Stainless Steel Blades Available
D36S
Ø1.9 mm - Ø36.0 mm
Aperture
D5S
Ø0.6 mm - Ø5.0 mm
Aperture
D25SZ
Ø0.0 mm - Ø25.0 mm
Aperture
D12SS
Ø1.0 mm - Ø12.0 mm Aperture
Stainless Steel
Leaves for High-Power
Applications

Please Wait
Iris Selection Guide |
---|
Post-Mountable Irises |
Unmounted Irises |
SM-Threaded Lever-Actuated Irises |
SM-Threaded Ring-Actuated Irises |
Cage System Irises |
Motorized Irises |
Features
- Choose from Three Versions:
- Standard Iris Diaphragms with Black Spring Steel Leaves
- Stainless Steel Leaves for High Power Applications
- Zero Aperture
- Continuously Variable Iris Diaphragms
- These Models Have No Mounting Holes
- Select Irises Sold in Packs of 5
These lever-actuated, continuously variable iris diaphragms are designed to provide smooth operation over many thousands of cycles. These irises do not have any mounting holes and cannot be attached directly to a post. Thorlabs also offers Post-Mountable irises, as well as SM-threaded Lever-Actuated and Ring-Actuated irises. In addition, we offer Cage System Irises for use with 30 mm and 60 mm cage systems. Select irises are also available in packs of five.
Insights into Aligning a Laser Beam
When installing a laser in an optical setup, it is good practice to start by leveling and orienting its beam so that it travels along a well-defined path. When the beam is prepared this way, not only is it easier to then divert the beam and route it through the optical elements in the system, but the results provided by tuning the system's alignment are more predictable and repeatable. The following sections describe how to:
- Level and Align the Laser Beam's Pointing Angle
- Divert the Beam and Align it to Follow a Desired Path
Click here for more Insights about lab practices and equipment.
Level and Align the Laser Beam's Pointing Angle
0:00 - Introduction
1:25 - Level and Align the Laser Beam's Pointing Angle
4:09 - Divert the Beam and Align it to Follow a Desired Path
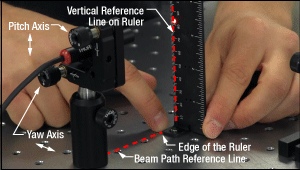
Click to Enlarge
Figure 196C The beam can be aligned to travel parallel to a line of tapped holes in the optical table. The yaw adjustment on the kinematic mount adjusts the beam angle, so that the beam remains incident on the ruler's vertical reference line as the ruler slides along the line of tapped holes.
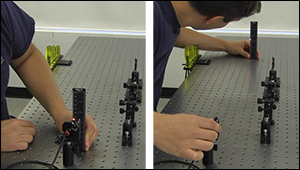
Click to Enlarge
Figure 196B Leveling the beam path with respect to the surface of an optical table requires using the pitch adjustment on the kinematic laser mount (Figure 196C). The beam is parallel to the table's surface when measurements of the beam height near to (left) and far from (right) the laser's front face are equal.
Pitch (tip) and yaw (tilt) adjustments provided by a kinematic mount can be used to make fine corrections to a laser beam's angular orientation or pointing angle. This angular tuning capability is convenient when aligning a collimated laser beam to be level with respect to a reference plane, such as the surface of an optical table, and when aligning with respect to a particular direction in that plane, such as along a line of tapped holes in the table.
Before Using the Mount's Adjusters
First, rotate each adjuster on the kinematic mount to the middle of its travel range. This reduces the risk of running out of adjustment range, and the positioning stability is frequently better when at the center of an adjuster's travel range.
Then, make coarse corrections to the laser's height, position, and orientation. This can be done by adjusting the optomechanical components, such as a post and post holder, supporting the laser. Ensure all locking screws are tightened after the adjustments are complete.
Level the Beam Parallel to the Table's Surface
Leveling the laser beam is an iterative process that requires an alignment tool and the fine control provided by the mount's pitch adjuster.
Begin each iteration by measuring the height of the beam close to and far from the laser (Figure 196B). A larger distance between the two measurements increases accuracy. If the beam height at the two locations differs, place the ruler in the more distant position. Adjust the pitch on the kinematic mount until the beam height at that location matches the height measured close to the laser. Iterate until the beam height at both positions is the same.
More than one iteration is necessary, because adjusting the pitch of the laser mount adjusts the height of the laser emitter. In Video 196A, for example, the beam height close to the laser was initially 82 mm, but it increased to 83 mm after the pitch was adjusted during the first iteration.
If the leveled beam is at an inconvenient height, the optomechanical components supporting the laser can be adjusted to change its height. Alternatively, two steering mirrors can be placed after the laser and aligned using a different procedure, which is detailed in the section. Steering mirrors are particularly useful for adjusting beam height and orientation of a fixed laser.
Orient the Beam Along a Row of Tapped Holes
Aligning the beam parallel to a row of tapped holes in the table is another iterative process, which requires an alignment tool and tuning of the mount's yaw adjuster.
The alignment tool is needed to translate the reference line provided by the tapped holes into the plane of the laser beam. The ruler can serve as this tool, when an edge on the ruler's base is aligned with the edges of the tapped holes that define the line (Figure 196C).
The relative position of the beam with respect to the reference line on the table can be evaluated by judging the distance between the laser spot and vertical reference feature on the ruler. Vertical features on this ruler include its edges, as well as the columns formed by different-length rulings. If these features are not sufficient and rulings are required, a horizontally oriented ruler can be attached using a BHMA1 mounting bracket.
In Video 196A, when the ruler was aligned to the tapped holes and positioned close to the laser, the beam's edge and the ends of the 1 mm rulings coincided. When the ruler was moved to a farther point on the reference line, the beam's position on the ruler was horizontally shifted. With the ruler at that distant position, the yaw adjustment on the mount was tuned until the beam's edge again coincided with the 1 mm rulings. The ruler was then moved closer to the laser to observe the effect of adjusting the mount on the beam's position. This was iterated as necessary.
Divert the Beam and Align it to Follow a Desired Path
The first steering mirror reflects the beam along a line that crosses the new beam path. A second steering mirror is needed to level the beam and align it along the new path. The procedure of aligning a laser beam with two steering mirrors is sometimes described as walking the beam, and the result can be referred to as a folded beam path. In the example shown in Video 196A, two irises are used to align the beam to the new path, which is parallel to the surface of the optical table and follows a row of tapped holes.
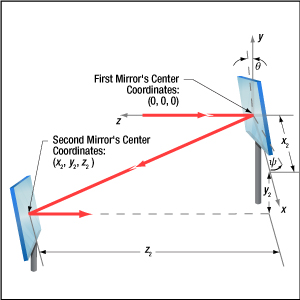
Click to Enlarge
Figure 196D The beam reflected from Mirror 1 will be incident on Mirror 2, if Mirror 1 is rotated around the x- and y-axes by angles θ and ψ, respectively. Both angles affect each coordinate (x2 , y2 , z2 ) of Mirror 2's center. Mirror 1's rotation around the x-axis is limited by the travel range of the mount's pitch (tip) adjuster, which limits Mirror 2's position and height options.
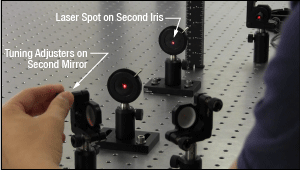
Click to Enlarge
Figure 196F The adjusters on the second kinematic mirror are used to align the beam on the second iris.
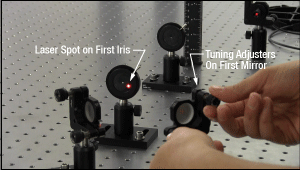
Click to Enlarge
Figure 196E The adjusters on the first kinematic mirror mount are tuned to position the laser spot on the aperture of the first iris.
Setting the Heights of the Mirrors
The center of the first mirror should match the height of the input beam path, since the first mirror diverts the beam from this path and relays it to a point on the second mirror. The center of the second mirror should be set at the height of the new beam path.
Iris Setup
The new beam path is defined by the irises, which in Video 196A have matching heights to ensure the path is level with respect to the surface of the table. A ruler or calipers can be used to set the height of the irises in their mounts with modest precision.
When an iris is closed, its aperture may not be perfectly centered. Because of this, switching the side of the iris that faces the beam can cause the position of the aperture to shift. It is good practice to choose one side of the iris to face the beam and then maintain that orientation during setup and use.
Component Placement and Coarse Alignment
Start by rotating the adjusters on both mirrors to the middle of their travel ranges. Place the first mirror in the input beam path, and determine a position for the second mirror in the new beam path (Figure 196D). The options are notably restricted by the travel range of the first mirror mount's pitch (tip) actuator, since it limits the mirror's rotation (θ ) around its x-axis. In addition to the pitch, the yaw (tilt) of the first mirror must also be considered when choosing a position
After placing the second mirror on the new beam path, position both irises after the second mirror on the desired beam path. Locate the first iris near the second mirror and the second iris as far away as possible.
While maintaining the two mirrors' heights and without touching the yaw adjusters, rotate the first mirror to direct the beam towards the second mirror. Adjust the pitch adjuster on the first mirror to place the laser spot near the center of the second mirror. Then, rotate the second mirror to direct the beam roughly along the new beam path.
First Hit a Point on the Path, then Orient
The first mirror is used to steer the beam to the point on the second mirror that is in line with the new beam path. To do this, tune the first mirror's adjusters while watching the position of the laser spot on the first iris (Figure 196E). The first step is complete when the laser spot is centered on the iris' aperture.
The second mirror is used to steer the beam into alignment with the new beam path. Tune the adjusters on the second mirror to move the laser spot over the second iris' aperture (Figure 196F). The pitch adjuster levels the beam, and the yaw adjuster shifts it laterally. If the laser spot disappears from the second iris, it is because the laser spot on the second mirror has moved away from the new beam path.
Tune the first mirror's adjusters to reposition the beam on the second mirror so that the laser spot is centered on the first iris' aperture. Resume tuning the adjusters on the second mirror to direct the laser spot over the aperture on the second iris. Iterate until the laser beam passes directly through the center of both irises, as shown in Video 196A. If any adjuster reaches, or approaches, a limit of its travel range, one or both mirrors should be repositioned and the alignment process repeated.
If a yaw axis adjuster has approached a limit, note the required direction of the reflected beam and then rotate the yaw adjuster to the center of its travel range. Turn the mirror in its mount until the direction of the reflected beam is approximately correct. If the mirror cannot be rotated, reposition one or both mirrors to direct the beam roughly along the desired path. Repeat the alignment procedure to finely tune the beam's orientation.
If a pitch axis adjuster has approached a limit, either increase the two mirrors' separation or reduce the height difference between the new and incident beam paths. Both options will result in the pitch adjuster being positioned closer to the center of its travel range after the alignment procedure is repeated.
Posted Comments: | |
user
 (posted 2020-01-31 06:03:10.787) The CAD file and drawing for this are incorrect.
More specifically - the adjustment lever is about 3/4mm longer than stated and a different shape MKiess
 (posted 2020-02-03 11:42:07.0) This is a response from Michael at Thorlabs. Thank you very much for this feedback. We will check this immediately and adjust the CAD drawings accordingly. user
 (posted 2016-02-11 14:27:51.693) Do the black spring steel leaves in the D25S shed any debris during extended operation? Is the black a coating or a metal treatment that would be less likely to wear off? shallwig
 (posted 2016-02-12 06:04:38.0) This is a response from Stefan at Thorlabs. Thank you very much for your inquiry. The “black” of the leaves comes from “Bluing” the steel which is a passivation process in which steel is partially protected against rust. Any debris during extended operation are not known so far. As you left no contact data could you please contact us at Europe@thorlabs.com for further questions. matz.liebel
 (posted 2015-04-10 16:36:18.06) We bought four of these irisis (before the warning that they can't be mounted was implemented) and I am still wondering what the point of this product is/was? "Unmountable" rather than "Unmounted" iris would certainly be a better product description.
Extremely disappointing lmorgus
 (posted 2015-04-10 12:13:23.0) A response from Laurie at Thorlabs to Matz: We apologize for the inconvenience our unmounted irises have caused you. They are often used by system integrators who are looking for a minimalistic design that they can either glue into position or machine a custom mount for. Your point is well taken that Unmountable might be a better descriptor than unmounted. We have updated the verbiage on our website in an effort to make this clearer. Thorlabs does sell some iris diaphragms that can be post mounted. We would be happy to exchange the ones you purchased for ones that incorporate a mounting feature. christian.Matzdorf
 (posted 2015-03-25 11:07:30.78) Why does the unmounted iris diafragma´s has no mounting hole? What can I do with this things if I am not able to mount them?!
So you force your Customer to order post mounted ones with a post which is not wanted each time. shallwig
 (posted 2015-03-26 04:29:29.0) This is a response from Stefan at Thorlabs. Thank you very much for your inquiry. These post mounted irises have a special setscrew which is glued into the iris. On request we also offer the irises without the post.
Regarding your question what you can do with the unmounted iris diaphragms. We have several mounts which can be used for holding these iris diaphragms, for example adjustable lens mounts like these http://www.thorlabs.com/newgrouppage9.cfm?objectgroup_id=54 or self-centering mounts http://www.thorlabs.com/newgrouppage9.cfm?objectgroup_id=1488 can be used. If you are more looking for a possibility to mount the iris on our SM1/2 tubes the ring-actuated Threaded Iris Diaphragms are an option.
http://www.thorlabs.com/newgrouppage9.cfm?objectgroup_ID=1479
I will contact you directly to discuss your needs in more detail. amilner
 (posted 2015-01-09 12:31:29.53) Hello, by mistake I have bought unmounted irises D20S instead of pre-mounted (recent sales order TS1294450). Can I buy mounting housing for them separately? Can you please give me the corresponding part number. Thank you. Alexander Milner. shallwig
 (posted 2015-01-12 03:22:51.0) This is a response from Stefan at Thorlabs. Thank you very much for you inquiry. Unfortunately the unmounted Irises of this series like the D20S do not have any mounting holes and cannot be attached directly to a post. We will contact you directly to exchange them by the pre-mounted Irises you were originally looking for. james.parker
 (posted 2014-04-11 14:11:59.133) Could you please tell me the centration tolerance of the minimum-sized aperture relative to the housing, the dimaensional tolerance of the housing and the depth of the iris plane within the housing for D8S. thank you. shallwig
 (posted 2014-04-16 09:02:36.0) This is a response from Stefan at Thorlabs. Thank you very much for your inquiry. Unfortunately, the centration tolerance is not specified but 0.25mm from the geometrical center is a reasonable estimate. The dimensional tolerances are as follows:
Outer diameter: +0.00 / - 0.05 mm
Thickness: +/- 0.1 mm
Depth of iris plane: 1.1 mm +/- 0.1 mm, measured from the front. scampbel
 (posted 2013-09-16 08:03:19.513) What is the power handling of these irises? What is "High Power" for the stainless steel? 1W or 1000W? Thanks- jlow
 (posted 2013-09-19 09:38:00.0) Response from Jeremy at Thorlabs: It’s hard to specify the laser damage threshold because it depends on several parameters such as wavelength, iris opening, exposure duration, etc. The maximum temperature that the blades can be heated would be around 250°C for the regular iris and around 400°C for the stainless steel version. mduquette
 (posted 2013-07-02 10:26:23.8) It would be extremely helpful if the travel of the arm in degrees were listed for all iris models. cdaly
 (posted 2013-07-02 16:34:00.0) Response from Chris at Thorlabs: Thank you for your feedback. If it is necessary to know the size of the aperture, we do have a graduated version, SM1D12C which has markings which denote the diameter of the opening for a given position. jlow
 (posted 2012-09-28 09:50:00.0) Response from Jeremy at Thorlabs: The thread size for the actuator lever on the D12S is M1.7x0.35mm. cjimenez
 (posted 2012-09-27 20:07:15.0) what is the thread size for the actuator lever on model D12S? bdada
 (posted 2011-12-13 13:36:00.0) Response from Buki at Thorlabs:
Thank you for your feedback. The iris diaphragms you asked about are our unmounted diaphragms, which are best for OEM applications that require custom mounting options. These unmounted diaphragms do not have mounting holes and cannot be mounted directly to a post.
To mount the iris, please consider our post mounted irises: http://www.thorlabs.com/NewGroupPage9.cfm?ObjectGroup_ID=206
The post mounted version of the D37SZ you asked about is the ID37Z Zero Aperture, Post-Mounted Iris Diaphragm, Ø37.0 mm Max Aperture
http://www.thorlabs.com/thorProduct.cfm?partNumber=ID37Z
For future reference, please note that we also provide SMx threaded irises: http://www.thorlabs.com/NewGroupPage9.cfm?ObjectGroup_ID=1479
If you have recently purchased the unmounted iris diaphragm and want to exchange it with one of the iris diaphragms that can be mounted, please contact TechSupport@thorlabs.com for further assistance. raphael.cohen3
 (posted 2011-12-11 06:11:00.0) we have a number of these
1/ is there a way to attach them to something?
2/ how can we use them without attaching them to anything?
thanks tor
 (posted 2010-11-29 14:50:19.0) Response from Tor at Thorlabs: The housing is CW614N brass, and the leaves are C100S+QT stainless steel. a.matveev
 (posted 2010-11-26 14:43:44.0) Which material is the frame of the diaphragm made of? |

- Black Spring Steel Leaves
- Continually Variable Iris Diaphragms
- These Items have No Mounting Holes
- Select Irises are Available in Packs of 5
Item # | Aperturea | Size (Outer Diameter) | Thickness |
---|---|---|---|
D5S | Ø0.6 mm - Ø5.0 mm (Ø0.02" - Ø0.20") | 0.40" (10.2 mm) | 0.18" (4.4 mm) |
D8S | Ø0.8 mm - Ø8.0 mm (Ø0.03" - Ø0.32") | 0.58" (14.8 mm) | 0.18" (4.5 mm) |
D12S | Ø1.0 mm - Ø12.0 mm (Ø0.04" - Ø0.47") | 0.78" (19.8 mm) | 0.20" (5.1 mm) |
D15S | Ø1.2 mm - Ø15.0 mm (Ø0.05" - Ø0.59") | 0.94" (24.0 mm) | 0.20" (5.0 mm) |
D20S | Ø1.2 mm - Ø20.0 mm (Ø0.05" - Ø0.79") | 1.18" (30.0 mm) | 0.22" (5.5 mm) |
D25S | Ø1.4 mm - Ø25.0 mm (Ø0.05" - Ø0.99") | 1.46" (37.0 mm) | 0.22" (5.6 mm) |
D36S | Ø1.9 mm - Ø36.0 mm (Ø0.06" - Ø1.42") | 1.96" (49.8 mm) | 0.23" (5.8 mm) |
D50S | Ø2.5 mm - Ø50.0 mm (Ø0.10" - Ø1.97") | 2.75" (69.9 mm) | 0.30" (7.5 mm) |
These irises do not have any mounting holes and cannot be attached directly to a post.Click here to view our full line of Post-Mountable Iris Diaphragms. |

- Stainless Steel Leaves, Suitable for High Power Applications
- Continuously Variable Iris Diaphragms
- These Items have No Mounting Holes
Item # | Aperturea | Size (Outer Diameter) | Thickness |
---|---|---|---|
D12SS | Ø1.0 mm - Ø12.0 mm (Ø0.04" - Ø0.47") | 0.78" (19.8 mm) | 0.20" (5.1 mm) |
D25SS | Ø1.4 mm - Ø25.0 mm (Ø0.06" - Ø0.99") | 1.46" (37.0 mm) | 0.22" (5.6 mm) |
These irises do not have any mounting holes and cannot be attached directly to a post.Click here to view our full line of Post-Mountable Iris Diaphragms. |

- Black Spring Steel Leaves
- Continuously Variable Iris Diaphragms
- Dual Layer Leaf Design Reduces Aperture to Zero When Closed
- These Items have No Mounting Holes
Item # | Aperturea | Size (Outer Diameter) | Thickness |
---|---|---|---|
D12SZ | Ø0.0 mm - Ø12.0 mm (Ø0.00" - Ø0.47") | 0.83" (21.0 mm) | 0.24" (6.2 mm) |
D25SZ | Ø0.0 mm - Ø25.0 mm (Ø0.00" - Ø0.98") | 1.50" (38.1 mm) | 0.24" (6.1 mm) |
D37SZ | Ø0.0 mm - Ø37.0 mm (Ø0.00" - Ø1.46") | 2.13" (54.0 mm) | 0.30" (7.5 mm) |
D50SZ | Ø0.0 mm - Ø50.0 mm (Ø0.00" - Ø1.97") | 2.84" (72.0 mm) | 0.36" (9.1 mm) |
D75SZ | Ø0.0 mm - Ø75.0 mm (Ø0.00" - Ø2.95") | 4.02" (102.1 mm) | 0.37" (9.4 mm) |
These irises do not have any mounting holes and cannot be attached directly to a post.Click here to view our full line of Post-Mountable Iris Diaphragms. |