Mounted Low-Order Wave Plates for MIR
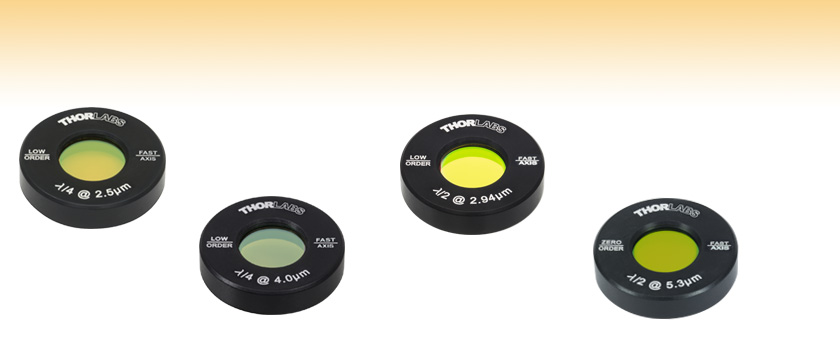
- Quarter- or Half-Wave Plates with Near Zero-Order Operation
- Seven Center Wavelengths Available Between 2.5 µm and 5.3 µm
- Ø1/2" Wave Plate in Ø1" Anodized Aluminum Housing
WPLQ05M-2500
2.5 µm Quarter-Wave Plate
WPLQ05M-4000
4.0 µm Quarter-Wave Plate
WPLH05M-2940
2.94 µm Half-Wave Plate
WPLH05M-5300
5.3 µm Half-Wave Plate

Please Wait
Common Specifications | |
---|---|
Substrate | Magnesium Fluoridea |
Clear Aperture | Ø10.0 mm (Ø0.39") |
Retardance Accuracy (Typical) | <λ/300 |
Beam Deviation | <10 arcsec |
Surface Quality | 40-20 Scratch-Dig |
Reflectance @ Design Wavelength (per Surface at 0° AOI) |
<0.25% |
Webpage Features | |
---|---|
![]() |
Clicking this icon in the tables below opens a window that contains specifications, performance graphs, and mechanical drawings. |
Features
- Seven Center Wavelengths Available: 2.5 µm, 2.713 µm, 2.94 µm, 3.5 µm, 4.0 µm, 4.5 µm, and 5.3 µm
- Low-Order, Quarter- and Half-Wave Plates Available
- AR Coated on Front and Back Optical Surface
- RoHS-Compliant Magnesium Fluoride Substrate
- Ø1/2" Wave Plates Within a Ø1" Housing
- Custom Options Available, Please Contact Tech Support for More Information
- OEM Pricing Available Upon Request
Thorlabs' low-order wave plates are made from a single piece of high-quality magnesium fluoride and provide either quarter-wave or half-wave retardance at one of seven center MIR wavelengths. Each wave plate is available as a Ø1/2" optic mounted in a Ø1" unthreaded housing. Half-wave plates are typically used to rotate the polarization of light, while quarter-wave plates are chosen if one wants to convert linearly polarized light into circularly polarized light.
Light passing through a low-order wave plate will undergo a low number of full or partial wavelength shifts (also referred to as the order, or m) in addition to the fractional design retardance. This differs from true zero-order and multi-order wave plates which undergo no shift or a high number of shifts, respectively. The low-order design maintains near zero-order performance making it a good alternative to true zero-order wave plates. The single magnesium fluoride substrate is also thinner compared to a zero-order design, which combines two multi-order wave plates, making our low-order retarders well suited for applications that are sensitive to dispersion. Our MIR quarter-wave plates have a retardance of either 3λ/4 or 5λ/4. Our MIR half-wave plates have a retardance of 3λ/2, with the exception of our WPLH05M-5300, which has a retardance of λ/2. Please note that a three-quarter-wave plate will circularly polarize a linearly polarized input beam in the opposite direction compared to a zero-order quarter-wave plate with the same fast-axis orientation.
Each wave plate is mounted in an anodized aluminum housing that is engraved with a line indicating the orientation of the fast axis of the wave plate. In addition, engraved text specifies the order of wave plate (i.e., low-order), whether it is a λ/4 or λ/2 wave plate, and the wavelength for which the wave plate was designed.
Thorlabs can also produce custom wave plates with no AR coating, a different AR coating, or a different design wavelength than those offered below. Please contact Tech Support with inquiries.
Mounting Options
The wave plates have an outer diameter of 12.7 +0/-0.1 mm, a mounted diameter of 25.4 mm (1.00"), and mounted thickness of 5.8 mm (0.23"). The Ø1" housing provides compatibility with our SM1-threaded products, such as rotation mounts, but require an SM1RR retaining ring for secure mounting.
The wave plates are easily removed from their mounts for use in custom or OEM applications; use an SPW603 SM05 Spanner Wrench to remove the retaining ring that secures the optic in the mount. The unmounted wave plates have two small flats parallel to the fast axis (see the image to the right). For further information on using and selecting a wave plate, please see our Wave Plate Selection Guide tab or contact Technical Support.
Operating Principle of Wave Plates
Optical wave plates are constructed from birefringent materials that have a difference in refractive index between two orthogonal axes. This birefringent property introduces a velocity difference between light polarized along the fast and slow principal axes of the wave plate. The fast principal axis of the wave plate has a lower refractive index, resulting in a faster velocity for light polarized in this direction. Conversely, the slow axis has a higher refractive index, resulting in a slower velocity for light with this polarization. When light passes through a wave plate, this velocity difference leads to a phase difference between the two orthogonal polarization components. The actual phase shift depends on the properties of the material, the thickness of the wave plate, and the wavelength of the signal, and can be described as:
where n1 is the refractive index along the slow axis, n2 is the refractive index along the orthogonal fast axis, d is the thickness of the wave plate, and λ is the signal wavelength.
Using a Wave Plate
Wave plates are typically available with a retardance of λ/4 or λ/2, meaning that a phase shift of a quarter wavelength or a half a wavelength (respectively) is created.
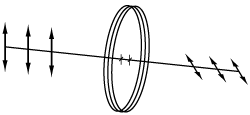
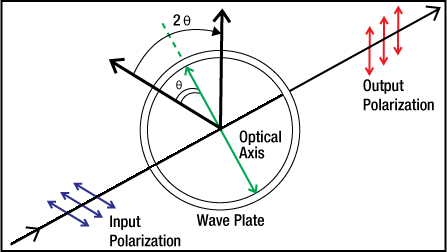
Half-Wave
As described above, a wave plate has two principal axes: fast and slow. Each axis has a different refractive index and, therefore, a different wave velocity. When a linearly polarized beam is incident on a half-wave plate, and the polarization of this beam does not coincide with one of these axes, the output polarization will be linear and rotated with respect to the polarization of the input beam (see image at right). When applying a circularly polarized beam, a clockwise (counterclockwise) circular polarization will transform into a counterclockwise (clockwise) circular polarization.
Half-wave (λ/2) plates are typically used as polarization rotators. Mounted on a rotation mount, a λ/2 wave plate can be used as a continuously adjustable polarization rotator, as shown below. Additionally, when used in conjunction with a Polarizing Beamsplitter a λ/2 wave plate can be used as a variable ratio beamsplitter.
The angle between the output polarization and the input polarization will be twice the angle between the input polarization and the wave plate’s axis (see diagram to the lower right). When the polarization of the input beam is directed along one of the axes of the wave plate, the polarization direction will remain unchanged.
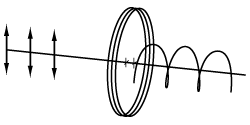
Quarter-Wave
A quarter-wave plate is designed such that the phase shift created between the fast and slow axes is a quarter wavelength (λ/4). If the input beam is linearly polarized with the polarization plane aligned at 45° to the wave plate's fast or slow axis, then the output beam will be circularly polarized (see image at right). If the linearly polarized beam is aligned at an angle other than 45°, then the output will be elliptically polarized. Conversely, the application of a circularly polarized beam to a λ/4 wave plate results in a linearly polarized output beam. Quarter wave plates are used in Optical Isolators, optical pumps, and EO Modulators.
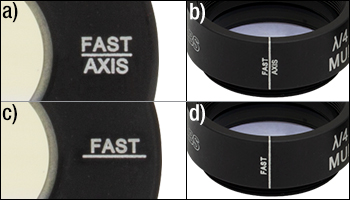
Click to Enlarge
Figure 1: Top Images (a,b): Engraving Reflects Updated Assembly Process as of October 2018; Bottom Images (c,d): Past Engraving
Fast and Slow Axis Identification
In October 2018, Thorlabs updated its wave plate assembly process and associated product engravings to be consistent with the IEEE/SPIE convention (see the Polarization Handedness Tutorial) for determining the fast and slow axes. By this convention, the current revisions of wave plates have the fast axis denoted by the “FAST AXIS” engraving visible in Figure 1 to the right. Although the location of the axes and the retardation value for each wave plate is easily determined, differentiating between the fast and slow axes is far more involved.
For most applications, the knowledge of whether an axis is fast or slow is not nearly as important as the retardation value. However, the fast/slow difference determines the left/right-hand circular polarization of light output from a quarter-wave plate, which can be important in applications such as atomic and solid state physics spectroscopy. To ensure the accuracy of our labeling moving forward, we have incorporated several redundant testing setups into our production processes, as described below.
Test Setup 1: Reflection Off Uncoated Metal with n > 1
This test setup is based on the method of Petre Logofatu1, which is also summarized well by Galgano and Henriques2. In this method, a light source passes through a generator, which is a linear polarizer oriented at 45° to the horizontal. Then, the light passes through the wave plate sample under test (SUT), is reflected off an uncoated metal surface (any metal with n > 1 will suffice), and passes through an analyzer (a second linear polarizer oriented at 90° to the generator). The light is then measured by a power sensor.
Our setup, shown in Figure 2 to the right, used a HeNe laser as the light source, two GTH10M-A Glan-Taylor polarizers as the generator and analyzer, a custom uncoated stainless steel reflective surface, an S120C power sensor, and a PM100D power meter console. A full parts list, except the custom metal surface and SUT, is provided below Figure 2.
As described by Logofatu, the power reflection coefficient, R in the equation below, can be derived from the Fresnel equations, showing that there will be a large difference in reflection off the metal depending on whether the fast or the slow axis of the SUT is horizontal.

Here, Rp and Rs represent the p-polarized and s-polarized components of R, Δ is the retardance of the SUT, and φ is the phase difference between the p and s reflection coefficients of the metallic surface. From this, we can determine which axis we would expect a higher reflection value when horizontal, and compare expected values to experimental values. Using a large angle of incidence allows for a large separation between s and p coefficients. This correlates with high versus low measured reflection, enabling easy determination of fast versus slow axis. As in both papers, the test was performed at a variety of angles. The results were then fitted to a theoretical curve.
The equation for R shown above differs from that in the Logofatu reference, in which we identified an error; our Reflection Coefficient Derivation PDF shows our own derivation of the Logofatu result.
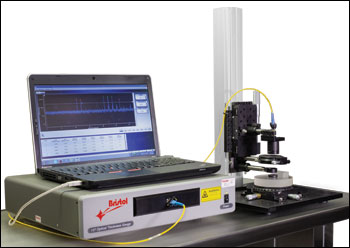
Click to Enlarge
Figure 3: Low Coherence Interferometry Wave Plate Testing Setup
Test Setup 2: Low Coherence Interferometry
This test setup uses low coherence interferometry to measure the optical path length (OPL) of the SUT as it is rotated, where the longest OPL corresponds with the slow axis, and the shortest OPL corresponds with the fast axis. This method is additionally verified by modifying the reference arm of the interferometer, adding a reference window and specular back surface to allow for calculation of the group index (ngSUT) along and normal to the crystal axis. These values can then be compared to known values, assuring the reliability of this test.
Our setup, shown in Figure 3 to the right, used a modified Bristol 157 Series Optical Gauge. As can be seen in Figure 4 below, the majority of the low coherence interferometer is contained within the chassis of the optical gaugea. The measurement arm is then modified with Thorlabs components, such that the fiber output can be aligned with a low NA objective, passed through a LPNIR100 linear polarizer and partially reflected off a WG11010 reference window, all mounted on a 34 mm rail. The light then reflects off the SUT and a custom specular back surface to send the interferometric signal back to the optical gauge.
The additional reference surfaces and resulting physical thickness are used to double check the validity of the results. This is done with a quick calculation to determine the group index of both the fast and slow axes. Figure 5 shows a qualitative representation of the output produced by this setup. Peaks 1 and 2 are created by the reference window, Peaks 3 and 4 by the SUT wave plate, while Peak 5 is generated by the reference surface. Thickness data from peak to peak are calculated by the software and output into a table. By first taking the distance from Peak 2 to Peak 5 before the wave plate is inserted, the total physical thickness, Tair0, is obtainedb. When inserting the wave plate, we can then take the distance from Peak 2 to 3, Tair1, and Peak 4 to 5, Tair2. Using this information we can easily calculate the thickness of the wave plate, TSUT by subtracting Tair1 and Tair2 from Tair0. Measuring the distance from Peak 3 to Peak 4 would give us OPLSUT. Dividing OPLSUT by TSUT produces the group index of the SUT, ngSUT. Comparing this group index to that provided in literature for quartz3 or MgF24 both along and normal to the crystal axis, we are in good agreement.
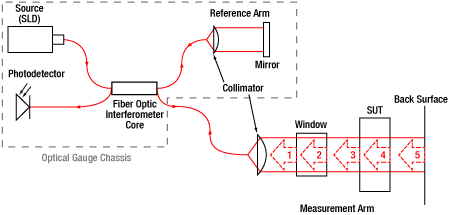
Click to Enlarge
Figure 4: Example Low Coherence Interferometry Diagram;
Numbered reflections in the measurement arm correspond with peak numbers in Figure 5.
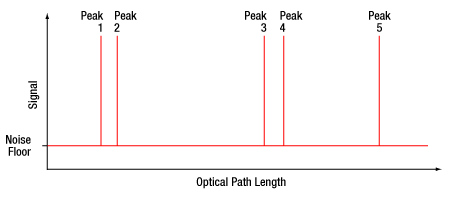
Click to Enlarge
Figure 5: Representation of Output from Optical Gauge
Damage Threshold Specifications | |
---|---|
Item # | Damage Threshold |
WPLQ05M-2940 WPLH05M-2940 |
50 J/cm2 (2940 nm, 250 µs, 2 Hz, Ø0.265 mm) |
Damage Threshold Data for Thorlabs' Mounted Low-Order Wave Plates
The specifications to the right are measured data for a selection of Thorlabs' mounted low-order wave plates.
Laser Induced Damage Threshold Tutorial
The following is a general overview of how laser induced damage thresholds are measured and how the values may be utilized in determining the appropriateness of an optic for a given application. When choosing optics, it is important to understand the Laser Induced Damage Threshold (LIDT) of the optics being used. The LIDT for an optic greatly depends on the type of laser you are using. Continuous wave (CW) lasers typically cause damage from thermal effects (absorption either in the coating or in the substrate). Pulsed lasers, on the other hand, often strip electrons from the lattice structure of an optic before causing thermal damage. Note that the guideline presented here assumes room temperature operation and optics in new condition (i.e., within scratch-dig spec, surface free of contamination, etc.). Because dust or other particles on the surface of an optic can cause damage at lower thresholds, we recommend keeping surfaces clean and free of debris. For more information on cleaning optics, please see our Optics Cleaning tutorial.
Testing Method
Thorlabs' LIDT testing is done in compliance with ISO/DIS 11254 and ISO 21254 specifications.
First, a low-power/energy beam is directed to the optic under test. The optic is exposed in 10 locations to this laser beam for 30 seconds (CW) or for a number of pulses (pulse repetition frequency specified). After exposure, the optic is examined by a microscope (~100X magnification) for any visible damage. The number of locations that are damaged at a particular power/energy level is recorded. Next, the power/energy is either increased or decreased and the optic is exposed at 10 new locations. This process is repeated until damage is observed. The damage threshold is then assigned to be the highest power/energy that the optic can withstand without causing damage. A histogram such as that below represents the testing of one BB1-E02 mirror.
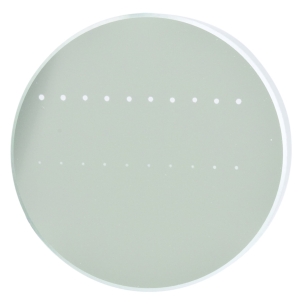
The photograph above is a protected aluminum-coated mirror after LIDT testing. In this particular test, it handled 0.43 J/cm2 (1064 nm, 10 ns pulse, 10 Hz, Ø1.000 mm) before damage.
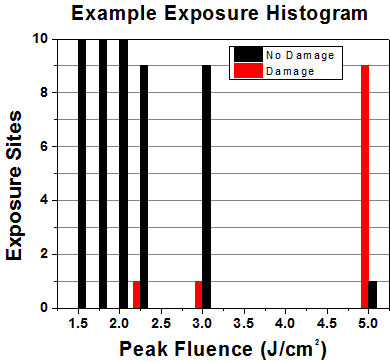
Example Test Data | |||
---|---|---|---|
Fluence | # of Tested Locations | Locations with Damage | Locations Without Damage |
1.50 J/cm2 | 10 | 0 | 10 |
1.75 J/cm2 | 10 | 0 | 10 |
2.00 J/cm2 | 10 | 0 | 10 |
2.25 J/cm2 | 10 | 1 | 9 |
3.00 J/cm2 | 10 | 1 | 9 |
5.00 J/cm2 | 10 | 9 | 1 |
According to the test, the damage threshold of the mirror was 2.00 J/cm2 (532 nm, 10 ns pulse, 10 Hz, Ø0.803 mm). Please keep in mind that these tests are performed on clean optics, as dirt and contamination can significantly lower the damage threshold of a component. While the test results are only representative of one coating run, Thorlabs specifies damage threshold values that account for coating variances.
Continuous Wave and Long-Pulse Lasers
When an optic is damaged by a continuous wave (CW) laser, it is usually due to the melting of the surface as a result of absorbing the laser's energy or damage to the optical coating (antireflection) [1]. Pulsed lasers with pulse lengths longer than 1 µs can be treated as CW lasers for LIDT discussions.
When pulse lengths are between 1 ns and 1 µs, laser-induced damage can occur either because of absorption or a dielectric breakdown (therefore, a user must check both CW and pulsed LIDT). Absorption is either due to an intrinsic property of the optic or due to surface irregularities; thus LIDT values are only valid for optics meeting or exceeding the surface quality specifications given by a manufacturer. While many optics can handle high power CW lasers, cemented (e.g., achromatic doublets) or highly absorptive (e.g., ND filters) optics tend to have lower CW damage thresholds. These lower thresholds are due to absorption or scattering in the cement or metal coating.
LIDT in linear power density vs. pulse length and spot size. For long pulses to CW, linear power density becomes a constant with spot size. This graph was obtained from [1].
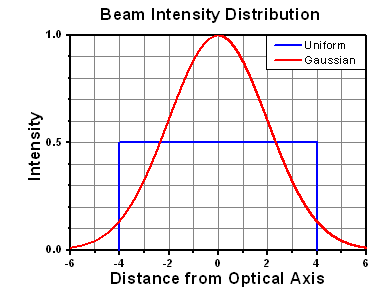
Pulsed lasers with high pulse repetition frequencies (PRF) may behave similarly to CW beams. Unfortunately, this is highly dependent on factors such as absorption and thermal diffusivity, so there is no reliable method for determining when a high PRF laser will damage an optic due to thermal effects. For beams with a high PRF both the average and peak powers must be compared to the equivalent CW power. Additionally, for highly transparent materials, there is little to no drop in the LIDT with increasing PRF.
In order to use the specified CW damage threshold of an optic, it is necessary to know the following:
- Wavelength of your laser
- Beam diameter of your beam (1/e2)
- Approximate intensity profile of your beam (e.g., Gaussian)
- Linear power density of your beam (total power divided by 1/e2 beam diameter)
Thorlabs expresses LIDT for CW lasers as a linear power density measured in W/cm. In this regime, the LIDT given as a linear power density can be applied to any beam diameter; one does not need to compute an adjusted LIDT to adjust for changes in spot size, as demonstrated by the graph to the right. Average linear power density can be calculated using the equation below.
The calculation above assumes a uniform beam intensity profile. You must now consider hotspots in the beam or other non-uniform intensity profiles and roughly calculate a maximum power density. For reference, a Gaussian beam typically has a maximum power density that is twice that of the uniform beam (see lower right).
Now compare the maximum power density to that which is specified as the LIDT for the optic. If the optic was tested at a wavelength other than your operating wavelength, the damage threshold must be scaled appropriately. A good rule of thumb is that the damage threshold has a linear relationship with wavelength such that as you move to shorter wavelengths, the damage threshold decreases (i.e., a LIDT of 10 W/cm at 1310 nm scales to 5 W/cm at 655 nm):
While this rule of thumb provides a general trend, it is not a quantitative analysis of LIDT vs wavelength. In CW applications, for instance, damage scales more strongly with absorption in the coating and substrate, which does not necessarily scale well with wavelength. While the above procedure provides a good rule of thumb for LIDT values, please contact Tech Support if your wavelength is different from the specified LIDT wavelength. If your power density is less than the adjusted LIDT of the optic, then the optic should work for your application.
Please note that we have a buffer built in between the specified damage thresholds online and the tests which we have done, which accommodates variation between batches. Upon request, we can provide individual test information and a testing certificate. The damage analysis will be carried out on a similar optic (customer's optic will not be damaged). Testing may result in additional costs or lead times. Contact Tech Support for more information.
Pulsed Lasers
As previously stated, pulsed lasers typically induce a different type of damage to the optic than CW lasers. Pulsed lasers often do not heat the optic enough to damage it; instead, pulsed lasers produce strong electric fields capable of inducing dielectric breakdown in the material. Unfortunately, it can be very difficult to compare the LIDT specification of an optic to your laser. There are multiple regimes in which a pulsed laser can damage an optic and this is based on the laser's pulse length. The highlighted columns in the table below outline the relevant pulse lengths for our specified LIDT values.
Pulses shorter than 10-9 s cannot be compared to our specified LIDT values with much reliability. In this ultra-short-pulse regime various mechanics, such as multiphoton-avalanche ionization, take over as the predominate damage mechanism [2]. In contrast, pulses between 10-7 s and 10-4 s may cause damage to an optic either because of dielectric breakdown or thermal effects. This means that both CW and pulsed damage thresholds must be compared to the laser beam to determine whether the optic is suitable for your application.
Pulse Duration | t < 10-9 s | 10-9 < t < 10-7 s | 10-7 < t < 10-4 s | t > 10-4 s |
---|---|---|---|---|
Damage Mechanism | Avalanche Ionization | Dielectric Breakdown | Dielectric Breakdown or Thermal | Thermal |
Relevant Damage Specification | No Comparison (See Above) | Pulsed | Pulsed and CW | CW |
When comparing an LIDT specified for a pulsed laser to your laser, it is essential to know the following:
LIDT in energy density vs. pulse length and spot size. For short pulses, energy density becomes a constant with spot size. This graph was obtained from [1].
- Wavelength of your laser
- Energy density of your beam (total energy divided by 1/e2 area)
- Pulse length of your laser
- Pulse repetition frequency (prf) of your laser
- Beam diameter of your laser (1/e2 )
- Approximate intensity profile of your beam (e.g., Gaussian)
The energy density of your beam should be calculated in terms of J/cm2. The graph to the right shows why expressing the LIDT as an energy density provides the best metric for short pulse sources. In this regime, the LIDT given as an energy density can be applied to any beam diameter; one does not need to compute an adjusted LIDT to adjust for changes in spot size. This calculation assumes a uniform beam intensity profile. You must now adjust this energy density to account for hotspots or other nonuniform intensity profiles and roughly calculate a maximum energy density. For reference a Gaussian beam typically has a maximum energy density that is twice that of the 1/e2 beam.
Now compare the maximum energy density to that which is specified as the LIDT for the optic. If the optic was tested at a wavelength other than your operating wavelength, the damage threshold must be scaled appropriately [3]. A good rule of thumb is that the damage threshold has an inverse square root relationship with wavelength such that as you move to shorter wavelengths, the damage threshold decreases (i.e., a LIDT of 1 J/cm2 at 1064 nm scales to 0.7 J/cm2 at 532 nm):
You now have a wavelength-adjusted energy density, which you will use in the following step.
Beam diameter is also important to know when comparing damage thresholds. While the LIDT, when expressed in units of J/cm², scales independently of spot size; large beam sizes are more likely to illuminate a larger number of defects which can lead to greater variances in the LIDT [4]. For data presented here, a <1 mm beam size was used to measure the LIDT. For beams sizes greater than 5 mm, the LIDT (J/cm2) will not scale independently of beam diameter due to the larger size beam exposing more defects.
The pulse length must now be compensated for. The longer the pulse duration, the more energy the optic can handle. For pulse widths between 1 - 100 ns, an approximation is as follows:
Use this formula to calculate the Adjusted LIDT for an optic based on your pulse length. If your maximum energy density is less than this adjusted LIDT maximum energy density, then the optic should be suitable for your application. Keep in mind that this calculation is only used for pulses between 10-9 s and 10-7 s. For pulses between 10-7 s and 10-4 s, the CW LIDT must also be checked before deeming the optic appropriate for your application.
Please note that we have a buffer built in between the specified damage thresholds online and the tests which we have done, which accommodates variation between batches. Upon request, we can provide individual test information and a testing certificate. Contact Tech Support for more information.
[1] R. M. Wood, Optics and Laser Tech. 29, 517 (1998).
[2] Roger M. Wood, Laser-Induced Damage of Optical Materials (Institute of Physics Publishing, Philadelphia, PA, 2003).
[3] C. W. Carr et al., Phys. Rev. Lett. 91, 127402 (2003).
[4] N. Bloembergen, Appl. Opt. 12, 661 (1973).
In order to illustrate the process of determining whether a given laser system will damage an optic, a number of example calculations of laser induced damage threshold are given below. For assistance with performing similar calculations, we provide a spreadsheet calculator that can be downloaded by clicking the button to the right. To use the calculator, enter the specified LIDT value of the optic under consideration and the relevant parameters of your laser system in the green boxes. The spreadsheet will then calculate a linear power density for CW and pulsed systems, as well as an energy density value for pulsed systems. These values are used to calculate adjusted, scaled LIDT values for the optics based on accepted scaling laws. This calculator assumes a Gaussian beam profile, so a correction factor must be introduced for other beam shapes (uniform, etc.). The LIDT scaling laws are determined from empirical relationships; their accuracy is not guaranteed. Remember that absorption by optics or coatings can significantly reduce LIDT in some spectral regions. These LIDT values are not valid for ultrashort pulses less than one nanosecond in duration.
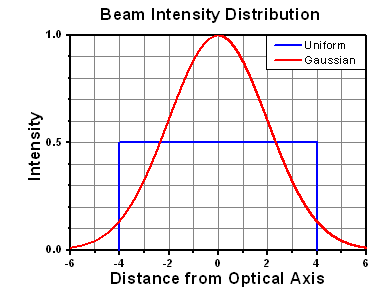
A Gaussian beam profile has about twice the maximum intensity of a uniform beam profile.
CW Laser Example
Suppose that a CW laser system at 1319 nm produces a 0.5 W Gaussian beam that has a 1/e2 diameter of 10 mm. A naive calculation of the average linear power density of this beam would yield a value of 0.5 W/cm, given by the total power divided by the beam diameter:
However, the maximum power density of a Gaussian beam is about twice the maximum power density of a uniform beam, as shown in the graph to the right. Therefore, a more accurate determination of the maximum linear power density of the system is 1 W/cm.
An AC127-030-C achromatic doublet lens has a specified CW LIDT of 350 W/cm, as tested at 1550 nm. CW damage threshold values typically scale directly with the wavelength of the laser source, so this yields an adjusted LIDT value:
The adjusted LIDT value of 350 W/cm x (1319 nm / 1550 nm) = 298 W/cm is significantly higher than the calculated maximum linear power density of the laser system, so it would be safe to use this doublet lens for this application.
Pulsed Nanosecond Laser Example: Scaling for Different Pulse Durations
Suppose that a pulsed Nd:YAG laser system is frequency tripled to produce a 10 Hz output, consisting of 2 ns output pulses at 355 nm, each with 1 J of energy, in a Gaussian beam with a 1.9 cm beam diameter (1/e2). The average energy density of each pulse is found by dividing the pulse energy by the beam area:
As described above, the maximum energy density of a Gaussian beam is about twice the average energy density. So, the maximum energy density of this beam is ~0.7 J/cm2.
The energy density of the beam can be compared to the LIDT values of 1 J/cm2 and 3.5 J/cm2 for a BB1-E01 broadband dielectric mirror and an NB1-K08 Nd:YAG laser line mirror, respectively. Both of these LIDT values, while measured at 355 nm, were determined with a 10 ns pulsed laser at 10 Hz. Therefore, an adjustment must be applied for the shorter pulse duration of the system under consideration. As described on the previous tab, LIDT values in the nanosecond pulse regime scale with the square root of the laser pulse duration:
This adjustment factor results in LIDT values of 0.45 J/cm2 for the BB1-E01 broadband mirror and 1.6 J/cm2 for the Nd:YAG laser line mirror, which are to be compared with the 0.7 J/cm2 maximum energy density of the beam. While the broadband mirror would likely be damaged by the laser, the more specialized laser line mirror is appropriate for use with this system.
Pulsed Nanosecond Laser Example: Scaling for Different Wavelengths
Suppose that a pulsed laser system emits 10 ns pulses at 2.5 Hz, each with 100 mJ of energy at 1064 nm in a 16 mm diameter beam (1/e2) that must be attenuated with a neutral density filter. For a Gaussian output, these specifications result in a maximum energy density of 0.1 J/cm2. The damage threshold of an NDUV10A Ø25 mm, OD 1.0, reflective neutral density filter is 0.05 J/cm2 for 10 ns pulses at 355 nm, while the damage threshold of the similar NE10A absorptive filter is 10 J/cm2 for 10 ns pulses at 532 nm. As described on the previous tab, the LIDT value of an optic scales with the square root of the wavelength in the nanosecond pulse regime:
This scaling gives adjusted LIDT values of 0.08 J/cm2 for the reflective filter and 14 J/cm2 for the absorptive filter. In this case, the absorptive filter is the best choice in order to avoid optical damage.
Pulsed Microsecond Laser Example
Consider a laser system that produces 1 µs pulses, each containing 150 µJ of energy at a repetition rate of 50 kHz, resulting in a relatively high duty cycle of 5%. This system falls somewhere between the regimes of CW and pulsed laser induced damage, and could potentially damage an optic by mechanisms associated with either regime. As a result, both CW and pulsed LIDT values must be compared to the properties of the laser system to ensure safe operation.
If this relatively long-pulse laser emits a Gaussian 12.7 mm diameter beam (1/e2) at 980 nm, then the resulting output has a linear power density of 5.9 W/cm and an energy density of 1.2 x 10-4 J/cm2 per pulse. This can be compared to the LIDT values for a WPQ10E-980 polymer zero-order quarter-wave plate, which are 5 W/cm for CW radiation at 810 nm and 5 J/cm2 for a 10 ns pulse at 810 nm. As before, the CW LIDT of the optic scales linearly with the laser wavelength, resulting in an adjusted CW value of 6 W/cm at 980 nm. On the other hand, the pulsed LIDT scales with the square root of the laser wavelength and the square root of the pulse duration, resulting in an adjusted value of 55 J/cm2 for a 1 µs pulse at 980 nm. The pulsed LIDT of the optic is significantly greater than the energy density of the laser pulse, so individual pulses will not damage the wave plate. However, the large average linear power density of the laser system may cause thermal damage to the optic, much like a high-power CW beam.
Posted Comments: | |
Chen zifeng
 (posted 2024-01-23 05:20:17.603) 你好,我想问一下这款波片写着中心波长为2.7μm,那它实际对光的作用范围大概在哪呢?比如我有一个光谱覆盖范围为2400-3200nm的脉冲光,可不可以利用这个四分之一波片和一个二分之一波片将脉冲的偏振态变为消光比比较好的线偏振光? jpolaris
 (posted 2024-02-09 12:07:03.0) 感谢您联系Thorlabs! 我们已直接与您联系分享我们WPLQ05M-2713波片的波长延迟量数据。这些波片无法将入射的非偏振光变为线偏振光,在本页面的“教程”标签中归纳总结了四分之一波片和半波片的背景信息。若您的目标是在 2400 nm - 3200 nm波长范围内将非偏振光变为高消光比的线偏振光,您可以考虑使用线栅偏振片、金红石晶体偏振片或纳米粒子薄膜偏振片,它们均可在下列链接中找到。对于线栅偏振片,我们提供在 2.25 µm - 4 µm 范围内消光比 > 10,000:1 的版本。对于金红石晶体偏振片 ,它在 2.2 µm - 4 µm 范围内可提供 100,000:1 的消光比。对于纳米粒子薄膜偏振片,我们提供在 2 µm - 4.5 µm 范围内消光比 >10,000:1 的版本。https://www.thorlabschina.cn/navigation.cfm?guide_id=24. || This feedback response is stating that they would like to convert a 2400 nm - 3200 nm laser source into a high extinction ratio linearly polarized source by using WPLQ05M-2713 and WPLH05M-2713. They also asked about the dependence on wavelength of the retardance. || Answer in English: Thank you for contacting Thorlabs. We have reached out to you directly with wavelength-dependent retardance data for WPLQ05M-2713. These quarter-wave and half-wave plates will not linearly polarize incident unpolarized light. If you would like an in-depth explanation about how quarter-wave and half-wave plates function, we provide background information about this on our Tutorial tab. If your goal is to linearly polarize incident unpolarized light over 2400 nm - 3200 nm, you might consider using a wire grid polarizer, a Rutile crystal polarizer, or a nanoparticle film polarizer, each of which can be found at the following link. For the wire grid polarizers, we offer versions with extinction ratios of > 10,000:1 over 2.25 µm - 4 µm. For the Rutile polarizers, these will provide an extinction ratio of 100,000:1 over 2.2 µm - 4 µm. Lastly, for the nanoparticle film polarizers, we offer versions with extinction ratios of >10,000:1 over 2 µm - 4.5 µm. https://www.thorlabs.com/navigation.cfm?guide_id=24 slou
 (posted 2016-10-25 17:18:57.113) Hi,
Greetings from Shuai. I am wondering whether this 4um half wave plate can also work well for a relatively broad MIR range, for instance, 2-6um. If not, will it generate an elliptical polarization for other wavelengths? what range can it work within?
Can the 5.3um half wave plate work for 6um light? The outcoming light will be linearly polarized or elliptically polarized?
Thanks a lot.
Shuai tfrisch
 (posted 2016-10-31 02:40:41.0) Hello, thank you for contacting Thorlabs. The retardance for other wavelengths can be seen by clicking the Specifications info button. I have contacted you directly with these plots attached. |
Choosing a Wave Plate
Thorlabs offers achromatic, superachromatic, zero-order (both unmounted wave plates and mounted wave plates), low-order, and multi-order wave plates (single wavelength and dual wavelength) with either λ/4 or λ/2 phase shift.
Achromatic Wave Plates provide phase retardance that is relatively independent of wavelength over a wide spectral range, and Superachromatic Wave Plates provide phase retardance almost entirely independent of wavelength over a much wider range than achromatic wave plates. In contrast, zero-order and multi-order wave plates provide a phase shift that is strongly wavelength dependent. Our achromatic wave plates are available with four operating ranges: 260 - 410 nm, 350 - 850 nm, 400 - 800 nm, 690 - 1200 nm, and 1100 - 2000 nm. Additionally, we offer superachromatic wave plates for the 310 - 1100 nm and 600 - 2700 nm ranges.
Round Zero-Order Wave Plate Comparison | ||
---|---|---|
Material | Quartz | LCP |
Sizes | Ø1/2" and Ø1" | Ø1/2", Ø1", and Ø2" |
Mounted Versions Available | Yes | Yes |
Retardances Available | 1/4 λ and 1/2 λ | 1/4 λ and 1/2 λ |
Retardance Accuracy | <λ/300 | <λ/100 |
Surface Quality | 20-10 Scratch-Dig | 60-40 Scratch-Dig |
Coating | V Coat | Broadband AR |
Coating Reflectance (per Surface) |
0.25% | <1.0% Average Over Specified Coating Range |
Zero-order wave plates are designed such that the phase shift created is exactly one quarter or one half of a wave. They offer substantially lower dependence on temperature and wavelength than multi-order wave plates. Our Zero-Order Quartz Half-Wave and Quarter-Wave Plates are composed of two wave plates stacked together with the fast axis of one aligned to the slow axis of the other to achieve zero-order performance. Thorlabs' zero-order wave plates are available for a number of discrete wavelengths ranging from 266 nm to 2020 nm. Our Polymer Zero-Order Half-Wave and Quarter-Wave Plates consist of a thin layer of liquid crystal polymer retarding material sandwiched between two glass plates and are available at discrete wavelengths between 405 nm and 2700 nm. Our quartz zero-order wave plates provide better retardance accuracy and lower reflectance (see table), while our LCP zero-order wave plates produce a smaller decrease in retardance at larger AOIs. In addition, Thorlabs also offers unmounted true Zero-Order Telecom Wave Plates for WDM applications.
MIR Wave Plates are made from a single piece of high-quality magnesium fluoride and provide either quarter-wave or half-wave retardance at 2.5 µm, 2.713 µm, 2.94 µm, 3.5 µm, 4.0 µm, 4.5 µm, or 5.3 µm. Light passing through these MIR wave plates will undergo a low number of full or partial wavelength shifts (also referred to as the order, or m) in addition to the fractional design retardance. This differs from true zero-order and multi-order wave plates which undergo no shift or a high number of shifts, respectively. The low-order design maintains near to true zero-order performance, making it a good alternative to true zero-order wave plates. The single magnesium fluoride substrate is also thinner compared to a zero-order design, which combines two multi-order wave plates, making our low-order retarders well suited for applications that are sensitive to dispersion.
Multi-Order Wave Plates are made such that the retardance of a light path will undergo a certain number of full wavelength shifts (also referred to as the order, or m) in addition to the fractional design retardance. Compared to their zero-order counterparts, the retardance of multi-order wave plates is more sensitive to wavelength and temperature changes. Multi-order wave plates are, however, a more economical solution for many applications where increased sensitivities are not an issue. Our multi-order wave plates are available for a number of discrete wavelengths ranging from 405 nm to 1550 nm. Thorlabs also offers Dual-Wavelength Multi-Order Wave Plates designed for use at both 532 nm and 1064 nm.
In addition to these options, Thorlabs also has the ability to design and manufacture custom wave plates for both OEM sales and individual low quantity orders. Our technical staff is able to help with all phases of your request: quoting, sales, and planning and manufacturing support. If you have a custom request or a question about our capabilities, please contact Tech Support to start a discussion.

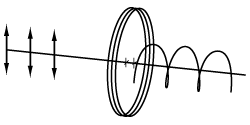
Quarter-wave plates can change linearly polarized light into circularly polarized light.
These wave plates feature a Ø10.0 mm (Ø0.39") clear aperture. They are compatible with our SM1-threaded rotation mounts when used with an SM1RR Retaining Ring. Please note that a three-quarter-wave plate will circularly polarize a linearly polarized input beam in the opposite direction compared to a zero-order quarter-wave plate with the same fast-axis orientation.

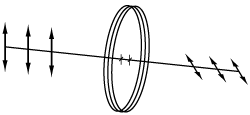
Half-wave plates can rotate the polarization plane of linearly polarized light.
These wave plates feature a Ø10.0 mm (Ø0.39") clear aperture. They are compatible with our SM1-threaded rotation mounts when used with an SM1RR Retaining Ring.